|
RICERCA TERMINE PER INIZIALE
ANODIZZAZIONE
ARIA
COMPRESSA
BURATTATURA
CARBONIO
( FIBRA )
COMPRESSORE
CORROSIONE
CROMATURA
EFFETTO
VENTURI
ELETTROEROSIONE
FRESATURA
Da
Wikipedia, l'enciclopedia libera.
L'alesatura è una
lavorazione meccanica per correggere lievemente
l'assialità e il diametro dei fori, chiamato alesaggio,
precedentemente realizzati con il trapano. Si esegue a
mano con gli alesatori montati sul giramaschi oppure a
macchina con l'alesatrice.
Il moto rotatorio dell'alesatore aumenta il diametro del
foro e lo porta pian piano al valore corretto,
eventualmente variando la posizione dell'asse. Per
alesare fori cilindrici e conici all'utensile viene
impresso un moto di traslatura parallela all'asse.
Per approfondire, vedi la voce officina (meccanica).
Caratteristiche
L'alesatura è un'operazione di finitura leggera, che
viene eseguita utilizzando un utensile multitagliente in
grado di lavorare fori con un'elevata precisione,
inoltre si ottengono ottime finiture superficiali e
tolleranze dimensionali strette, le quali sono ottenute
con un'elevata velocità d'avanzamento, ma questa
lavorazione deve essere eseguita con un foro prelavorato
entro limiti stretti, dato che la profondità del taglio
radiale dell'utensile deve essere piccola.
Alesatura a mano
Si usano alesatori a mano con codolo ad attacco quadro
montati sul giramaschi a manubrio, meglio se regolabile.
Si accosta l'imbocco dell'utensile al foro e lo si
introduce con attenzione di una quantità sufficiente a
garantirne la guida e l'assialità, poi si ruota
l'utensile in senso orario applicando una leggera spinta
parallela all'asse per agevolare la traslazione nel foro
che deve procedere con regolarità e senza strappi o
impuntamenti. Nel caso di fori passanti bisognerà
procedere sin quando l'utensile non sia completamente
uscito dalla parte opposta; per i fori ciechi bisognerà
invece impiegare una serie di alesatori di diametro via
via crescente. La lubrificazione con olio da taglio o
altro opportuno lubrificante è sempre consigliata,
soprattutto nel caso di fori lunghi o qualora s'intenda
allargare sensibilmente il diametro. A fine lavoro si
ripulisce tutto con aria compressa assicurandosi che il
truciolo sia completamente evacuato.
Per fori a sezione quadrata o rettangolare o comunque
non rotonda si usano speciali alesatori chiamati brocce
e l'operazione prende il nome di brocciatura.
STAMPA
SABBIATRICI - ALESATURA

TORNA
MENU GLOSSARIO
Da
Wikipedia, l'enciclopedia libera.
L'anodizzazione (detta
anche ossidazione anodica) è un processo elettrochimico
irreversibile mediante il quale uno strato protettivo di
ossido di alluminio si forma sulla superficie del
particolare trattato e lo protegge dalla corrosione. Nel
materiale avviene una vera e propria trasformazione
superficiale: il metallo nudo reagisce con l'ossigeno
che si sviluppa all'anodo durante il processo di
elettrodeposizione e forma ossido di alluminio o
allumina. Lo strato di materiale formato è variabile (normalmente
10 µm), esistono due tipi di ossidazione anodica: quella
sottile che comporta uno stato variabile dagli 8 ai 20
micron e quella dura che comporta uno strato dai 20 ai
50 micron.
Fasi del trattamento
Il trattamento è costituito dai seguenti passaggi:
sgrassaggio , eventuale satinatura chimica, depatinatura,
ossidazione anodica, neutralizzazione, eventuale colore,
fissaggio e asciugatura.
STAMPA
SABBIATRICI - ANODIZZAZIONE

TORNA
MENU GLOSSARIO
ARIA
COMPRESSA
Da
Wikipedia, l'enciclopedia libera.
L'aria compressa è aria
atmosferica compressa con un compressore alternativo o
con una pompa e immagazzinata in un serbatoio oppure
utilizzata subito. Serve per azionare utensili
pneumatici e per soffiare, gonfiare, ripulire da polvere
o limatura metallica. Talvolta è deumidificata prima di
raggiungere il serbatoio con un deumidificatore
installato all'uscita del compressore per scongiurare la
condensa, che può causare ruggine e danni ai
servomeccanismi. Dal serbatoio si distribuisce con
tubature di plastica o metallo (di solito rame) verso i
regolatori di pressione e i rubinetti a valvola a sfera
dai quali si preleva con tubazioni flessibili per gli
usi più disparati. Presso il serbatoio e i rubinetti di
distribuzione è comune trovare manometri per il
controllo della pressione e valvole di sicurezza.
Eventuali nebulizzatori d'olio lubrificano i meccanismi
degli utensili grazie al trasporto di minute goccioline
attraverso l'aria.
Per l'hobbystica sono disponibili piccoli compressori
trasportabili e bombolette spray.
Utilizzo
L'aria compressa si usa in innumerevoli casi. Per
esempio in officina per azionare utensili automatici
come la pistola avvitatrice oppure per gonfiare gli
pneumatici degli autoveicoli o per pulire, anche per
verniciare a spruzzo; in falegnameria per utensili come
la pistola sparachiodi; nei laboratori di ottica per la
sospensione dei tavoli antivibrazioni e per la pulizia
delle superfici ottiche; nelle macchine utensili per
l'azionamento di valvole e martinetti; nei cantieri
edilizi per i martelli pneumatici. Molto nota è la pompa
per bicicletta, a mano o a pedale. Ormai quasi scomparsa
ma un tempo assai diffusa è la posta pneumatica: l'aria
spinge un recipiente che contiene ll lettere o altri
oggetti attraverso un sistema di tubi fino al
destinatario. Si fa notare che l'aria compressa è
utilizzata largamente nel mondo ferroviario per
l'attuazione del sistema frenante e per innumerevoli
altri usi (porte automatiche, toilette).
STAMPA
SABBIATRICI - ARIA COMPRESSA

TORNA
MENU GLOSSARIO
Da
Wikipedia, l'enciclopedia libera.
La
burattatura (o barilatura) è una lavorazione meccanica
di finitura superficiale.
Tipicamente usata per la rimozione meccanica di residui
di substrato, in particolare bava, dovuti alla
lavorazione come stampaggio, fusione. Particolarmente
adatta per dare una finitura superficiale ad un numero
elevato di pezzi, di piccole dimensioni.
Avviene per rotolamento e urto dei pezzi in un barile (buratto)
ed eventualmente di materiale abrasivo sagomato allo
scopo, che velocizza l'operazione. Eventualmente la
lavorazione può essere fatta pure in immersione di
liquido, con lo scopo di prevenire attacchi chimici. La
velocita di rotazione del barile influenza la rapidità
di lavorazione.
STAMPA
SABBIATRICI - BURATTATURA

TORNA
MENU GLOSSARIO
Da
Wikipedia, l'enciclopedia libera.
Fibra di carbonio
Un tessuto costituito da
filamenti di carbonio intrecciati.La fibra di carbonio è
una struttura filiforme, molto sottile, realizzata in
carbonio con la quale si costruiscono una grande varietà
di materiali detti compositi in quanto le fibre sono "composte"
ovvero unite assieme ad una matrice, in genere di resina
(ma può essere in metallo o in plastica) la cui funzione
è quella di tenere in "posa" le fibre resistenti (affinché
mantengano la corretta orientazione nell'assorbire gli
sforzi), di proteggere le fibre ed inoltre di mantenere
la forma del manufatto composito. Per la realizzazione
di strutture in composito le fibre di carbonio vengono
dapprima intrecciate insieme a organizzare veri e propri
panni in tessuto di carbonio e poi, una volta messi in
posa, vengono immersi nella matrice. Tra le sue
caratteristiche spiccano l'elevata resistenza meccanica,
la bassa densità, la capacità di isolamento termico,
resistenza a variazioni di temperatura e all'effetto di
agenti chimici, buone proprietà ignifughe. Di contro il
materiale risulta non omogeneo e presenta spesso una
spiccata anisotropia, ovvero le sue caratteristiche
meccaniche hanno una direzione privilegiata.
Storia
La prima fibra di carbonio ad alte prestazioni fu creata
dal Dr. Roger Bacon, fisico e scienziato dei materiali
presso il Parma Technical Center, Ohio, nel 1958. Il
materiale creato da Bacon consisteva principalmente in
sottili filamenti di grafite disposti in fogli o in
rotoli; i fogli si estendevano in modo continuo
sull'intera lunghezza del filamento di grafite. Dopo
avere sviluppato la fibra di carbonio, Bacon stimò il
costo della produzione di fibre ad alta prestazione a
"10 milioni di dollari per libbra". Il materiale creato
da Bacon rappresentò una scoperta di notevole rilievo a
quell'epoca, e gli scienziati e gli industriali furono
determinati nel trovare una metodica produttiva
efficiente e meno costosa.
Il 14 gennaio 1969 la Carr Reinforcements produsse il
primo tessuto in fibra di carbonio esistente al mondo.
Sintesi
Un metodo comune per
ottenere i filamenti di carbonio consiste
nell'ossidazione e pirolisi termica del
poliacrilonitrile (PAN), un polimero a base di
acrilonitrile utilizzato anche per la produzione di
materie plastiche. Il PAN viene riscaldato
approssimativamente alla temperatura di 300 °C in
presenza di aria, con il risultato di ottenere
l'ossidazione e la rottura di molti legami idrogeno
instauratisi tra le lunghe catene polimeriche. Il
prodotto dell'ossidazione viene quindi posto in una
fornace e riscaldato a circa 2000 °C in atmosfera di gas
inerte, come quella di argon, ottenendosi in tal modo un
cambiamento radicale della struttura molecolare con
formazione di grafite. Effettuando il processo di
riscaldamento nelle corrette condizioni richieste, si ha
la condensazione delle catene polimeriche con produzione
di ristretti fogli di grafene che eventualmente possono
fondersi generando un singolo filamento. Il risultato
finale consiste solitamente nell'ottenimento di un
materiale con contenuto in carbonio variabile tra il
93-95%. Fibre di qualità inferiore possono essere
prodotte utilizzando pece o rayon quali precursori in
sostituzione del PAN. Le proprietà meccaniche della
fibra di carbonio possono essere ulteriormente
migliorate sfruttando opportuni trattamenti termici.
Riscaldando nell'intervallo di 1500-2000 °C (carbonizzazione)
si ottiene un materiale con il più alto carico di
rottura (5650 MPa), mentre la fibra di carbonio
riscaldata a 2500-3000 °C (grafitizzazione) mostra un
modulo di elasticità superiore (531 GPa).
Struttura e proprietà
Un filamento di carbonio
del diametro di 6 μm (che si estende da sinistra in
basso a destra in alto) a confronto con un capello
umano.Le fibre di carbonio hanno proprietà molto simili
all'asbesto. Ogni intreccio di filamenti di carbonio
costituisce un insieme formato dall'unione di molte
migliaia di filamenti. Un singolo tale filamento ha
sottile forma cilindrica del diametro di 5-8 μm e
consiste quasi esclusivamente di carbonio.
La struttura atomica della fibra di carbonio è simile a
quella della grafite, consistendo in aggregati di atomi
di carbonio a struttura planare (fogli di grafene)
disposti secondo simmetria esagonale regolare. La
differenza consiste nel modo in cui questi fogli sono
interconnessi. La grafite è un materiale cristallino in
cui i fogli sono disposti parallelamente l'uno rispetto
all'altro formando una struttura regolare. I legami
chimici che si instaurano tra i fogli sono relativamente
deboli, conferendo alla grafite la sua caratteristica
delicatezza e fragilità. In funzione della materia prima
utilizzata per produrre la fibra, la fibra di carbonio
può essere turbostratica o grafitica, ovvero possedere
una struttura ibrida in cui sono presenti sia parti
turbostratiche che grafitiche. Nella fibra di carbonio
turbostratica, ovvero con struttura cristallina formata
da piani ciascuno deviato lateralmente rispetto
all'altro, i fogli di atomi di carbonio sono uniti in
modo casuale o ripiegati insieme. Le fibre di carbonio
ottenute dal PAN sono turbostratiche, mentre le fibre di
carbonio derivate dalla mesofase pece sono grafitiche
dopo riscaldamento a temperature superiori a 2200 °C. Le
fibre di carbonio turbostratiche tendono ad avere
maggior carico di rottura, mentre le fibre derivate
dalla mesofase pece sottoposte a trattamento termico
possiedono elevata elasticità (modulo di Young) ed
elevata conducibilità termica.
Usi
La fibra di carbonio è
prevalentemente utilizzata per rinforzare i materiali
compositi, in particolar modo i polimeri plastici. Un
altro utilizzo sfrutta il conferimento di un certo
valore estetico a vari prodotti di consumo.
Sfruttandone le caratteristiche di resistenza e
leggerezza del peso, la fibra di carbonio viene
utilizzata per la produzione delle casse degli orologi e
del quadrante. Nella fabbricazione degli orologi, il
materiale è spesso combinato con un polimero per
aumentarne la resistenza.
Materiali non polimerici possono essere utilizzati anche
in funzione di matrice per le fibre di carbonio. A causa
della formazione di carburi (per esempio il carburo di
alluminio, idrosolubile) e a problematiche legate a
fenomeni di corrosione, l'utilizzo del carbonio in
compositi a matrice metallica è poco sviluppato. Il
carbonio-carbonio (RCC, Reinforced Carbon-Carbon)
consiste in un rinforzo di fibra di carbonio in una
matrice di grafite e viene utilizzato in applicazioni
che richiedono l'esposizione a temperature elevate, come
nel caso degli scudi termici dei veicoli spaziali o dei
freni delle auto di Formula 1. Questo materiale è
utilizzato anche per la filtrazione di gas ad alta
temperatura, come elettrodo a elevata area superficiale
e resistente alla corrosione, e come componente
antistatico.
La fibra di carbonio è utilizzata anche nei recipienti
per gas compressi, inclusi quelli per l'aria compressa.
Molto raramente si usano lastre piane di composito
piegandole a caldo, viene infatti preferita al tecnica
di polimerizzazione delle resine direttamente su uno
stampo, impregnando ogni strato di tela di fibra alla
volta, spesso comprimendo il tutto per migliorare
l'uniformità dello spessore
Industria tessile
In relazione al loro
modulo di elasticità, esistono differenti categorie di
fibre di carbonio: con modulo basso (fino a 200 GPa),
modulo standard (200-250 GPa), modulo intermedio
(250-325 GPa) e modulo elevato (>325 GPa).[6] La
resistenza meccanica dei differenti tipi di filato varia
tra 2-7 GPa. La densità tipica della fibra di carbonio è
1750 kg/m3.
Gli intrecci di filamenti di fibra di carbonio sono
utilizzati in diversi processi, tra i quali spiccano il
rinforzo di materiale plastico, la tessitura dei
filamenti e la pultrusione. Il filato di fibra di
carbonio viene classificato in base alla sua densità
lineare (peso per unità di lunghezza, con 1 g / 1000 m =
1 tex) o in base al numero di filamenti per filato. Per
esempio 200 tex per 3000 filamenti di fibra di carbonio
sono tre volte resistenti rispetto a 1000 fibre di
carbonio, ma anche tre volte più pesanti. Questo filato
può essere utilizzato per creare vari tessuti, il cui
aspetto dipende generalmente dalla densità lineare del
filato e dal tipo di tessitura eseguita. Alcuni tipi di
tessuti comunemente utilizzati sono la saia, il raso e
la tela.

TORNA
MENU GLOSSARIO
CARBURO
DI
TUNGSTENO
Da Wikipedia, l'enciclopedia libera.
Il
carburo di tungsteno è una lega ampiamente utilizzata
nell’industria e le sue caratteristiche vengono
sfruttate in vari settori. La sua alta capacità di
taglio e resistenza ne fanno un’ottima lega per la
produzione di utensili da taglio e truciolatura.
Nasce naturalmente con la combinazione tra carbonio e
tungsteno, due elementi che miscelati tra di loro sotto
forma di polvere devono subire il processo di
carburizzazione, con temperature da 1550 a 2500°C. A
loro vengono aggiunti elementi come il cromo o il
tantalio per evitare la crescita delle polveri, fungendo
da inibitori. Dopo di che le polveri formate subiscono 3
passaggi:
Macinazione, per mescolare tra di loro polveri di
diversa qualità e creare una miscela omogenea di polveri
Riscaldamento a 100°C con aggiunta di legante (cobalto)
per formare una massa solida grazie all’unione dei
granelli
Sinterizzazione a 1600°C per consentire al cobalto di
fondere, saldare i grani ed eliminare le porosità.
STAMPA
SABBIATRICI - CARBURO DI TUNGSTENO

TORNA
MENU GLOSSARIO
Da
Wikipedia, l'enciclopedia libera.
Il compressore è una macchina pneumofora che innalza la
pressione di un gas mediante l'impiego di energia
meccanica.
I compressori possono dividersi in due famiglie:
compressori volumetrici e compressori dinamici. Nell'uso
comune, si definisce ventilatore un compressore per aria
a bassa o bassissima pressione (fino a 10 kPa); questi
sono trattati in un articolo apposito. Sono compressori
anche alcuni tipi di pompe a vuoto, anche queste
trattate in apposito articolo.
Il compressore si distingue in genere dalla pompa in
quanto agisce su un fluido definito comprimibile, ossia
per il quale valga, almeno approssimativamente, la legge
dei gas perfetti (PV = nRT).
Nel seguito viene citato il rapporto di compressione.
Questo è definito come rapporto tra la pressione
assoluta di mandata e la pressione assoluta di ingresso,
in unità coerenti. ed è quindi un numero puro,
usualmente espresso in forma frazionaria (ad esempio con
2 : 1 si intende un rapporto di compressione pari a 2).
Compressore a vite
Nel compressore a vite, due viti a passo inverso e di
diametro differente imboccano l'una sull'altra, in modo
da creare una cavità che progressivamente si sposta
dalla zona di aspirazione a quella di mandata,
comprimendo così il gas. Rispetto ai compressori
alternativi hanno il vantaggio di una meccanica più
semplice - il moto è continuo - e quindi minori
sollecitazioni meccaniche. Si possono ottenere rapporti
di compressione minori, ma comunque elevati (3 : 1 - 4 :
1), ed è comunque possibile porre più stadi in serie. Il
rendimento meccanico è superiore agli alternativi, e
quindi per applicazioni medio-grandi sono preferibili a
questi ultimi.
STAMPA
SABBIATRICI - COMPRESSORE

TORNA
MENU GLOSSARIO
Da Wikipedia, l'enciclopedia libera.
La corrosione è un processo di
degradazione e ricomposizione con altri elementi a cui
sono soggetti i metalli. Questi si trovano ad un livello
energetico maggiore di quello a cui stanno i
corrispondenti minerali e, in determinate condizioni
ambientali, sono soggetti a corrosione.
Il processo di corrosione avviene secondo diversi
meccanismi chimico/fisici.
Corrosione chimica o in ambiente secco
Porta in ferro con evidenti segni di corrosioneÈ una
corrosione chimica, che si manifesta quando un metallo è
immerso in un'atmosfera gassosa di natura diversa da
quella normale (cloro, acidi, ossigeno secco ecc.),
oppure uguale ma ad elevata temperatura, le due
condizioni si possono avverare contemporaneamente,
favorendo così la corrosione. Le condizioni esterne (atmosfera,
temperatura ecc.) e la natura del metallo possono creare
una sottile pellicola di ossido stabile, dallo spessore
di qualche μm, al di sotto della quale prosegue la
diffusione dell'ossigeno.
Si ha corrosione puramente chimica quando un metallo è
immerso, in assenza di umidità, in un’atmosfera gassosa
di natura diversa da quella normale oppure normale ma ad
elevata temperatura: le due condizioni si possono
verificare contemporaneamente favorendo la corrosione.
Le condizioni esterne e la natura del metallo possono
creare una sottile pellicola stabile (passivazione) che
cessa non appena sono varcati i limiti dello stato di
equilibrio.
La formazione di ossidi di ferro è la conseguenza della
permanenza eccessiva di un acciaio a temperatura elevata
in un ambiente ossidante.
Durante il raffreddamento in aria si forma un
rivestimento fragile costituito da 3 ossidi.
La ruggine è quindi costituita da uno strato di ossidi
che non protegge l’acciaio sottostante dal procedere
della corrosione perché tale strato è friabile e non
sufficientemente aderente. Nel caso di rame o alluminio,
l’ossido ha un peso specifico minore del peso specifico
del metallo stesso, quindi, a parità di peso l’ossido
occupa maggior volume e quindi protegge il materiale
sottostante. Nel caso dell’acciaio, invece, l’ossido ha
un peso specifico maggiore del peso specifico del
metallo stesso, quindi, a parità di peso l’ossido occupa
minor volume e si ritira e crea delle crepe dove penetra
altro ossigeno che continua il processo corrosivo nella
parte sottostante. Pertanto la pellicola di ossido di
ferro non può essere considerata protettiva.
Aspetti termodinamici
L'affinità chimica di tutti i metalli, tranne l'oro, per
l'ossigeno a temperatura ambiente è positiva e in
seguito diminuisce all'aumentare della temperatura. Ne
consegue che vi è sempre la tendenza a formare ossidi,
più o meno stabili a seconda dell'intervallo di
temperatura.
Se poi si considera una lega, si hanno casi diversi:
ossidazione del metallo soluto, se questo ha un'affinità
per l'ossigeno maggiore e la diffusione di quest'ultimo
nella lega è buona;
ossidazione del metallo solvente: si forma uno strato di
ossido del solvente con all'interno particelle del
soluto;
ossidazione di entrambi.
serie elettrochimica
Aspetti cinetici
Si considerano qui i fattori che intervengono sulla
velocità di accrescimento dello strato di ossido:
rapporto tra il volume dell'ossido che si forma e quello
del metallo base ossidato, che determina lo stato del
film di ossido: tensionato, in leggera compressione,
raggrinzito;
all'aumentare della temperatura diminuisce l'energia
liberata dal metallo nel processo di corrosione e quindi
l'energia che può passare all'ossigeno molecolare
affinché si dissoci in atomico e si leghi agli atomi
metallici. In generale, comunque, la velocità aumenta
con la temperatura, ma non sempre con andamento lineare;
si preferiscono quindi metalli che obbediscono alle
leggi logaritmiche e cubiche (alluminio e sue leghe,
aggiunte di cromo);
la permeabilità all'ossigeno e la conducibilità
elettrica dell'ossido.
Corrosione intercristallina (o intergranulare)
Si manifesta ai bordi dei grani di una soluzione solida,
in particolare dell'acciaio inossidabile austenitico o
ferritico che sia stato sensibilizzato con un
riscaldamento oltre i 500°C.
In queste condizioni infatti si ha la precipitazione dei
carburi di cromo, i quali, grazie all'alta temperatura,
diffondono verso le zone distorte (i bordi dei grani),
dove vi è una maggiore concentrazione di carbonio.
Si crea così una situazione di bordi dei grani ricchi di
carburi di cromo, che fungono da catodo, e di matrice
circostante con Cr < 12%, non più passivata e quindi
fungente da anodo: può così iniziare la corrosione a
umido. Una grana fine in questa situazione è
controproducente, in quanto una maggiore estensione dei
bordi dei grani implica maggiore estensione delle zone
sottoposte a corrosione.
Per ridurre tale corrosione è consigliabile attraversare
velocemente l'intervallo critico di temperatura (per
esempio con raffreddamento in acqua) oppure prolungare
il riscaldamento: questo per impedire o favorire la
diffusione del cromo. Un'ulteriore soluzione, adottata
spesso negli acciai inossidabili austenitici, è
aggiungere in lega quantità relativamente piccole di
metalli più carburabili del cromo (Ti, Cb o Ta), che,
formando i propri carburi, impediscono la carburazione
del cromo.
Una soluzione largamente diffusa consiste nel
decarburare l'acciaio, portando la percentuale di
carbonio al di sotto dello 0,03%, così da limitare la
formazione di carburi di cromo; questi materiali sono
contraddistinti dalla sigla "L" (Low Carbon).
Corrosione galvanica o elettrochimica o in ambiente
umido
Il fenomeno della corrosione galvanica o elettrochimica
si ha quando due materiali di diverso potenziale
elettrico (nobiltà differente), vengono posti a diretto
contatto tra di loro, in presenza di un terzo elemento (elettrolito).
Le reazione che avvengono durante il processo di
corrosione sono tutte redox.
In questa situazione si genera un flusso di elettroni
dal materiale meno nobile (avente potenziale maggiore),
denominato anodo o polo positivo che si ossida, verso
quello più nobile avente potenziale minore, denominato
catodo o polo negativo che si riduce.
Pertanto si riscontra un aumento della velocità di
corrosione del materiale meno nobile (per esempio zinco,
ferro, nichel) e una diminuzione della velocità
dell’attacco corrosivo del materiale più nobile (per
esempio rame, argento, acciaio inox).
I concetti alla base della corrosione per contatto
galvanico di metalli possono essere estesi anche agli
accoppiamenti di metalli e leghe con materiali da loro
differenti, quali ossidi e solfuri, purché dotati di
conducibilità elettronica (per esempio magnetite,
solfuri di rame e ferro, grafite).
L'entità della corrosione dipende:
dalla diffferenza di potenziale che si crea tra i due
elementi e che è tanto più grande quanto più distanti
sono gli elementi stessi nella scala dei poteziali
standard (scala galvanica o nobiltà);
dalla quantità di ossigeno presente nell'ambiente;
dal rapporto tra la superficie complessiva dei due
metalli e qualla del metallo meno nobile.
La nobiltà relativa dei diversi materiali metallici non
risulta essere univocamente definita dai valori
termodinamici riportati nella serie elettrochimica dei
potenziali di equilibrio di ossidoriduzione per le
reazioni di ionizzazione dei vari metalli.
È necessario, infatti, conoscere anche i valori dei
potenziali che i diversi materiali assumono una volta
immersi in ambienti aggressivi “reali”, stabilendo in
questo modo delle serie galvaniche “pratiche”, relative
al comportamento dei vari materiali metallici qualora
vengano accoppiati nei differenti ambienti in esame.
La nobiltà di un materiale metallico può infatti variare
in un ampio intervallo di potenziale in dipendenza delle
condizioni sia dell’ambiente (composizione, valore di
pH, temperatura, presenza o assenza di condizioni di
scambio termico, agitazione,…) che del materiale
metallico (passività a seguito della presenza di film
superficiali protettivi o attività quando la superficie
metallica è direttamente a contatto con il mezzo
aggressivo).
In termini applicativi, la realizzazione di
accoppiamenti di materiali prossimi tra loro nelle serie
galvaniche dovrà essere considerata favorevole,
risultando questi materiali tra loro “galvanicamente
compatibili”, mentre dovrà essere il più possibile
evitato l’impiego di materiali tra loro lontani nella
serie galvanica d’interesse.
Nel processo di corrosione per contatto, in qualche caso
può verificarsi un’inversione di polarità della coppia
per cui il materiale inizialmente si comporta da catodo
e viceversa.
Un esempio classico è quello della coppia Zn-Fe in acque
naturali a temperatura elevata; lo zinco, metallo meno
nobile e inizialmente anodico rispetto al ferro, a
seguito della formazione di un film passivante stabile
di ossido di zinco dotato di conducibilità elettronica,
assumerà nel tempo un comportamento catodico rispetto al
ferro.
Tra i fattori che regolano la corrosione per contatto va
ricordata la conducibilità elettrica dell’ambiente
aggressivo. Infatti, nei mezzi dotati di elevata
conducibilità l’attacco è intenso e si fa sentire a
distanze elevate, mentre in ambienti con alta
resistività la corrosione risulta limitata alla zona
anodica in prossimità della giunzione con l’area
catodica. Per tale motivo questo tipo di corrosione
risulta particolarmente grave in acque di mare ma non in
acque dolci che hanno una conducibilità di almeno due
ordini di grandezza più bassa.
Un altro fattore importante nella regolazione della
corrosione galvanica è rappresentato dal rapporto tra le
aree catodiche e quelle anodiche; le condizioni più
sfavorevoli si realizzano quando l’area anodica è
piccola rispetto a quella catodica, in quanto l’attacco
corrosivo si concentra sull’area limitata. Un esempio
tipico può essere l’impiego di elementi di giunzione in
ferro (chiodi o viti) su strutture in rame.
La prevenzione o il contenimento della corrosione per
contatto possono essere realizzati evitando il contatto
tra materiali di nobiltà molto diversa o isolando tra
loro, ove possibile, materiali metallici differenti.
Anche l’impiego di rivestimenti protettivi o di
inibitori può ridurre il rischio di corrosione per
contatto. Qualora sia impossibile evitare l’impiego di
una coppia di materiali metallici tra loro non
compatibili, si può ampliare la catena galvanica,
introducendo un terzo metallo, meno nobile di quelli
costituenti la coppia, agente quindi come anodo
sacrificabile.
Nobiltà dei metalli
I metalli sono caratterizzati da una loro nobiltà, che
indica la maggiore o minor facilità dei materiali a
cedere un certo numero di elettroni.
I metalli più nobili (rame, argento, ecc) cedono più
difficilmente gli elettroni che non i metalli meno
nobili (ferro, zinco, ecc.).
Dal punto di vista puramente qualitativo qui di seguito
viene riportata la scala galvanica (riferita
all'elettrodo ad idrogeno) dei più comuni metalli e
leghe (partendo dal meno nobile):
Litio
Sodio
Magnesio
Titanio
Alluminio
Manganese
Zinco
Cromo
Ferro - (Acciaio al carbonio, Ghisa)
Cadmio
Nichel
Stagno
Piombo
Rame
Acciaio inox
Argento
Mercurio
Platino
Oro
Corrosione del ferro e delle sue leghe (acciao e
ghisa)
La condizione necessaria affinchè si manifesti la
corrosione elettrochimica del ferro, a temperatura
normale, è che il manufatto si trovi in presenza di
acqua e ossigeno.
In un metallo X isolato, immerso in una soluzione
acquosa, avviene naturalmente la seguente reazione:
X → Xn+ + ne-
Questo significa che X ha la tendenza a far passare in
soluzione alcuni atomi diposti sulla sua superficie
sotto forma di ioni Xn+.
Poichè gli ioni che passano in soluzione lasciano nel
metallo i loro elettroni più esterni ne-, il metallo
stesso si carica negativamente.
In questa situazione alcuni ioni Xn+ verranno attratti
dal metallo e si ridepositeranno sulla sua superficie in
forma metallica secondo la reazione:
Xn+ + ne- → X
Quando le due reazioni raggiungono la stessa velocità si
ha un equilibrio dinamico, cioè il numero di atomi che
lasciano il metallo è uguale al numero di ioni che si
ridepositano su questo.
A questo punto Il metallo assumerà un determinato
potenziale elettrico (potenziale di ossidoriduzione).
Qualora, in presenza di un elettrolito, due metalli (o
parti dello stesso metallo) a diverso potenziale vengono
messi a contatto, si forma una cella galvanica o pila.
Il suddetto processo dipende dalla natura chimico-fisico
del metallo e dal tipo di ambinete in cui è immerso.
Sulla superficie dei manufatti in acciaio, a causa delle
lavorazioni subite, vi sono sempre zone o punti che
differiscono tra loro fisicamente o chimicamente e che
pertanto hanno un diverso potenziale; .
Tra due di questi punti, nonostante la differenza di
potenziale (ΔE), non vi è però passaggio di corrente se
l'ambiente è secco, anche in presenza di ossigeno, non
potendosi realizzare un conduttore ionico.
Se invece sulla superficie del manufatto si deposita uno
strato di acqua o un leggero velo di umidità,
normalmente contenuta nell'atmosfera, tra i due punti
con differenza di potenziale si vengono a costituire
miriadi di minuscole pile, poichè:
si genera un circuito ionico che si effettua nel velo di
acqua o umidità (conduttore di seconda specie)
si genera un circuito elettronico che si effettua nel
ferro (conduttore di prima specie).
L'acqua infatti a causa del suo carattere anfotero è
debolmente dissociata in ioni idrogeno H+ e ossidrili
OH-:
H2O → H+ + OH-.
Pertanto, anche se l'acqua è purissima, presenta una
piccola ma misurabile conducibilità elettrica.
Per quanto sopra la corrosione nel ferro segue il
seguente processo.
Nella zona anodica, il ferro passa in soluzione cedendo
all'acqua o al velo di umidità, lo ione Fe++ e liberando
nel contempo degli elettroni:
2Fe → 2Fe++ + 4e-.
Gli elettroni liberati dagli atomi di ferro in
corrispondenza dell'anodo, migrano attraverso il metallo
(circuito elettronico) al catodo, dove reagiscono con
gli ioni idrogeno H+ provienienti dal circuito ionico:
4H+ + 2e- → 2H2
Questo ha un duplice effetto:
in primo luogo, venendo meno ioni idorgeno nel velo
d'acqua aumenta la concetrazioni di ioni ossidrilli OH-
e pertanto l'area catodica diviene alcalina
in secondo luogo, la formazione di gas idrogeno tende a
polarizzare ed inibire ulteriori reazioni. Il mantello
gassoso che si forma rallenta l'avvicinamento di molti
ioni idrogeno verso la zona catodica e ostacola la fuga
di nuovi elettroni da essa.
A questo punti interviene l'ossigeno presente nell'acqua
o nel velo di umidità reagendo con il gas idrogeno, con
formazione di acqua, che depolarizza il catodo:
2H2 +O2 → 2H2O.
Nel contempo nella zona anodica gli ioni ossidrili
provenienti dal catodo attraverso il circuito ionico,
incontrano gli ioni ferrosi Fe++ che si diffondono
dall'anodo nell'acqua o nel velo di umidità, con
formazioni di idrato ferroso:
2Fe++ + 4OH- → 2Fe(OH)2
In presenza di sufficiente ossigeno nella zona anodica,
lo ione ferroso viene ossidato a ione ferrico con
formazione di ossido ferrico idrato ( che costituisce
chimicamente la ruggine), poco solubile, che precipita
sul metallo:
2Fe(OH)2 +½O2 →Fe2O3.nH2O + H2O.
Data la tendenza degli ioni ferrosi a diffondersi
dall'anodo prima di combinarsi e formare la ruggine,
questa depositatasi sulla superficie del manufatto in
ferro, si presenta come un prodotto spugnoso con labile
adesione sul metallo all'anodo.
Pertanto la sua azione protettiva (passivazione) non è
sufficiente a inibire od arrestare il processo corrosivo
come avverrebbe se i prodotti dell'ossidazione fossero
perfettamente aderenti e compatti.
La continua perdita di metallo all'anodo può verificare
profonde cavità e persino la perforazione dello stesso
elemento in acciaio.
Quanto su detto vale per l'azione dell'acqua e
dell'ossigeno sulla corrosione dell'acciaio.
Nel caso si è in presena di elettroliti, il processo di
corrosione è accelerato.
questo avviene per esempio in atmosfera marina o in
acqua di mare.
In questa situazione resta valido il meccanismo visto
precedentemente, ma gli ioni ferrosi che si diffondono
dall'anodo si combinano più facilmente con gli ioni
cloro prodotti dalla dissociazione elettrolitica del
cloruro di sodio nell'acqua o nel velo di umidità,
formando cloruro ferroso:
4NaCl → 4Na+ + 4Cl-
2Fe++ + 4Cl- → 2FeCl2.
Contemporaneamente nella zona catodica gli ioni sodio si
combinano con gli ioni ossidrilli (OH-) formando idrato
di sodio: 4Na+ +4OH- → 4NaOH.
La successiva reazione tra cloruro ferroso, idrato di
sodio e l'ossigeno, presente nell'acqua o nel velo
d'umidità, determina la formazione di ossido ferrico:
4FeCl2 + NaOH + O2 → 2Fe2O3 + 8NaCl + 4H2O
Poichè anche in questa caso sia il cloruro ferroso che
l'idrato sodico sono molto solubili, diffondendosi nel
circuito ionico sia nella zona anodica che catodica, la
ruggine che desposita sulla superficie del materiale
ferroso risulta ancora molto spugnosa e molto labile e
pertanto non riesce a passivare il metallo.
Inoltre il processo di corrosione è ulteriormente
facilitato dalla rigenerazione del cloruro di sodio.
Metodi di protezione dalla corrosione
Per arrestare la corrosione si possono utilizzare una
protezione di tipo passivo e/o di tipo attivo.
Nel primo caso la protezione serve ad isolare la
superficie del metallo dall'ambiente esterno mediante il
suo rivestimento (previo accurata pulizia della stessa)
con ad esempio:
un film di pittura protettiva;
manti a base di polietilene o bitume, frequentemente
usati come rivestimento esterno delle tubazioni in
acciaio interrate.
prodotti di ossidazione ottenuti ad esempio mediante
l'ossidazione anodica, utilizzata per metalli come
l'alluminio, il nichel o il cobalto. Gli ossidi di
questi materiali sono molto tenaci ed aderenti allo
strato superficiale e pertanto passivano il metallo.
metalli meno nobili, quali lo zinco. In questo caso si
parla della zincatura, usata per proteggere il ferro,
effettuata immergendo il metallo, in un bagno fuso di
zinco. In questo caso, poichè lo zinco è più riducente
del ferro, anche se un parte della superficie ferrosa
rimane scoperta, l'ossidazione procede sullo zinco (con
formazione di ruggine bianca costituita prevalentemente
da idrossido di zinco e in minima parte da ossido e
carbonato)e il ferro rimane protetto fino a quando non è
stato consumato tutto lo zinco.
metalli più nobili, quali il cromo. In questo caso si
parla di cromatura che viene utilizzata per proteggere i
manufatti di ferro. Il rivestimento della superficie del
ferro avviene per lo più per via elettrolitica.
Le protezioni attive sono chiamate protezioni catodiche
e sono uilizzate per eliminare i fenomemi di corrosione
dei manufatti di ferro interrati.
Si possono distinguer due tipologie di protezioni
catodiche:
a corrente impressa: consiste nell'applicare
dall'esterno una fem contraria, ossia collegare il
manufatto al polo negativo di un generatore esterno il
cui polo positivo è a sua volta collegato ad un
elettrodo inerte (esempio grafite) interrato in
prossimità del manufatto. L'umidità del terreno funge da
elettrolita.
ad anodo sacrificale o ad accoppiamento galvanico:
consiste nel collegare direttamente il maufatto in ferro
ad un elettrodo interrato costituito da un metallo meno
nobile (più riducente) del ferro stesso, quali lo zinco
o il magnesio. Si viene a creare una cella galvanica in
cui il ferro funge da catodo e l'elettrodo da anodo che
di conseguenza si corrode preservando così l'integrità
del manufatto in ferro fino a quando l'anodo non si
consuma completamente.
STAMPA
SABBIATRICI - CORROSIONE

TORNA
MENU GLOSSARIO
Da
Wikipedia, l'enciclopedia libera.
La cromatura è un
rivestimento di cromo su un manufatto di ferro o acciaio
per proteggerlo.
Procedimento
La cromatura può essere effettuata in vari modi:
Procedimento galvanico
Cromatura a spessore ottenuta tramite processo galvanico,
per ridare un determinato spessore ad un oggetto, sempre
di ferro o acciaio, consumatosi durante l'utilizzo e
rendendolo idoneo al reimpiego, sfruttando le
caratteristiche di durezza del cromo, previa rettifica
del pezzo stesso.
Questo procedimento é utilizzato ad esempio, negli
inserti mobili degli stampi per l'estrusione
dell'argilla, nell'industria laterizia, che si consumano
per il continuo sfregamento con l'impasto di terra
estruso ad alte pressioni.
Il processo di cromatura tradizionale (in uso nel campo
dell'arredamento) prevede l'immersione del pezzo da
cromare in una serie di bagni. In una prima serie di
questi il pezzo viene sgrassato e pulito perfettamente.
Tra questi si ricordano i principali: soluzione
elettrolitica di soda caustica, soluzione elettrolitica
di acido cloridrico con relativi bagni di lavaggio. Il
bagno principale (dove il pezzo sosta più a lungo) è
quello della soluzione elettrolitica di nichel. Nei
fatti, prima del riporto di cromo, è importante creare
uno strato di nichel che uniforma il più possibile la
superficie metallica a livello microscopico. Dopo un
ulteriore lavaggio avviene l'immersione nella vasca
della soluzione elettrolitica del cromo. Negli ultimi
anni, oltre al cromo esavalente, si usa sempre di più il
cromo trivalente, definito 'ecologico'. Esiste poi la
cromatura satinata (opaca) per la quale il processo è
simile tranne che per l'ultimo bagno dove, con l'uso di
particolari olii, si creano delle microbolle
uniformemente distribuite sulla superficie del pezzo che
danno il caratteristico aspetto opaco alla superficie
stessa.
Vantaggi
Riduzione della corrosione, esso infatti avendo un
potenziale meno elettronegativo dell'acciaio limita la
formazione di micropile all'azione anodica molto modesta
dei giunti dei grani.
Indurimento superficiale del materiale il cromo essendo
un metallo molto duro viene usato su elementi che devono
resistere a forti usure, come le forcelle, inoltre
questo fino ai anni '50 è stato usato per rivestire i
cilindri in alluminio dei motori, ma poi è stato
sostituito da Ni-Kasil perché risultò ancora migliore e
perché non tende a sfogliarsi quando si usura.
Svantaggi
In caso di rotture o porosità del film protettivo, il
metallo sottostante si corrode in maniera localizzata e
molto intensa (si ricordi, per esempio, la degradazione
di molte parti metalliche cromate nelle automobili con
qualche decennio di vita).
Resta fondamentale, di conseguenza, un adeguato spessore
della cromatura, il cui valore minimo dipende dal
metallo da proteggere, dalle condizioni ambientali e da
fattori economici.
Insorgere di tensioni residue di trazione sulla
superficie del materiale base, ciò può portare a
degradare le qualità meccaniche del materiale nella vita
a fatica o peggio ancora la possibilità di innescare
fenomeni auto-esaltanti di corrosione e fatica.
STAMPA
SABBIATRICI - CROMATURA

TORNA
MENU GLOSSARIO
EFFETTO VENTURI
Da Wikipedia, l'enciclopedia libera.
L'effetto Venturi (o
paradosso idrodinamico) è il fenomeno fisico, scoperto e
studiato dal fisico Giovanni Battista Venturi, per cui
la pressione di una corrente fluida aumenta con il
diminuire della velocità.
È possibile studiare la variazione di pressione di un
liquido in un condotto, inserendo dei tubi manometrici.
L'esperimento dimostra che il liquido raggiunge nei tubi
altezze diverse: minore dove la sezione si
rimpicciolisce (in cui aumenta la velocità) e maggiore
quando la sezione si allarga (ovvero quando la velocità
diminuisce). Dato che la pressione del liquido aumenta
all'aumentare dell'altezza raggiunta dal liquido nei
tubi manometrici, è possibile dire che ad un aumento
della velocità corrisponde una diminuzione della
pressione e viceversa, cioè all'aumento della pressione
corrisponde una diminuzione della velocità.
Con esperimenti appropriati, è possibile notare lo
stesso fenomeno nei gas.
Esempio di diminuzione della pressione in un tratto di
condotta che presenta una strozzaturaConsideriamo una
generica condotta che presenti una diminuzione della sua
sezione e chiamiamo A1 l'area maggiore e A2 l'area
minore. Dall'equazione di continuità applicata alla
fluidodinamica sappiamo che la portata entrante nella
prima sezione deve essere esattamente uguale a quella
passante per la seconda. Da ciò, poiché la portata può
essere espressa come prodotto della velocità del fluido
per la sezione in cui passa, sappiamo che c'è un aumento
di velocità nella sezione A2 rispetto a quella in A1 (v1
< v2).
Sulla base di queste considerazioni, supponendo che non
esista una differenza di quota tra le due sezioni, è
possibile utilizzare come sistema di riferimento per le
altezze l'asse della condotta, eliminando in questo modo
un termine nell'equazione di Bernoulli, che si
presenterà in questa forma:
con ρ=densità; p=pressione; v=velocità del flusso.
Si può notare, quindi, che all'aumentare della velocità
del fluido si crea necessariamente una diminuzione della
pressione interna al fluido stesso. Nel caso del nostro
esempio, cioè, la pressione p2 risulterà essere minore
della pressione p1.
Il paradosso idrodinamico
Effetto VenturiL'Effetto Venturi viene anche chiamato
paradosso idrodinamico poiché si può pensare che la
pressione aumenti in corrispondenza delle strozzature;
tuttavia, per la legge della portata, la velocità
aumenta in corrispondenza delle strozzature. Quindi se
abbiamo un tubo che finisce contro una piastra come in
figura e il fluido ha una pressione leggermente
superiore alla pressione atmosferica, l'aumento di
velocità che la strozzatura crea tra tubo e piastra farà
aumentare la velocità a scapito della pressione del
fluido. Se la pressione scende al di sotto della
pressione atmosferica, la piastra tenderà a chiudere il
tubo anziché volare via. Da questo nasce il paradosso
idrodinamico che è una conseguenza della Legge di
Bernoulli.
STAMPA
SABBIATRICI - EFFETTO VENTURI

TORNA
MENU GLOSSARIO
Da
Wikipedia, l'enciclopedia libera.
L'elettroerosione è una tecnologia di lavorazione ad
asportazione di truciolo che utilizza le capacità
erosive delle scariche elettriche. Per la particolarità
del principio, questa tecnologia è in grado di lavorare
solo materiali fortemente conduttori; essenzialmente i
metalli.
Le macchine utensili realizzate per eseguire questo tipo
di lavorazione vengono chiamate 'macchine per
elettroerosione', o in inglese EDM (Electro Discharge
Machining).
Inventata casualmente dai coniugi sovietici Lazarenko
nel 1943, durante esperimenti sull'usura dei contatti
elettrici. Immergendo i contatti per diminuirne l'usura
in un bagno d'olio ottennero l'effetto contrario.
L'elettroerosione ha subito un forte impulso solo con lo
sviluppo dell'elettronica. Per le sue caratteristiche
peculiari, oggi è una tecnologia di uso comune
nell'industria, e addirittura necessaria nella
produzione stampi (in particolar modo per componenti in
plastica).
Una delle aziende che ha maggiormente contribuito nello
sviluppo di questa tecnica è l'AGIE di Losone in
Svizzera fondata nel 1954, con oltre 50 anni di storia
nel settore e oltre un migliaio di brevetti. Ancor oggi
leader nel settore.
Nel corso degli anni i processi si sdoppiarono tra
elettroerosione a tuffo (EDM) e elettroerosione a filo
(WEDM)
Caratteristiche della lavorazione
Le principali caratteristiche della lavorazione per
elettroerosione sono:
Possibilità di lavorare metalli molto duri (acciai
speciali, acciai rapidi, metalli duri, ecc...), o
induriti con trattamenti termici o chimici (temprati,
carburati, ecc...). Infatti, la durezza del materiale da
lavorare ha un'influenza secondaria per quanto riguarda
la velocità d'asportazione o l'energia da utilizzare
nella lavorazione.
Possibilità di lavorare il pezzo creandovi qualsiasi
figura geometrica o volumetrica. Ciò è dovuto alla
particolarità che l'elettroerosione non necessita di un
utensile rotante. È possibile ottenere spigoli netti,
creare nervature e cavità con forme o profili
impossibili da realizzare con altre tecnologie.
Velocità di lavorazione molto lenta rispetto alle altre
tecnologie ad asportazione di truciolo.
Elevata usura relativa dell'utensile. Un valore tipico
può essere 1-5%; cioè l'usura di 1-5 mm-cubi di utensile
ogni 100 mm-cubi di materiale asportato.
Le superfici lavorate presentano sempre un certo grado
di rugosità (più o meno pronunciato, a seconda del grado
di finitura). Questo è dovuto alla creazione di
micro-crateri che sono il risultato dell'azione
elettroerosiva (vedi sotto principio fisico).
Funzionamento
L'azione di lavorazione si attua avvicinando un utensile
(definito elettrodo) al materiale da lavorare (definito
pezzo), il tutto in un ambiente riempito da un
dielettrico liquido. L'elettrodo viene alimentato con
polarità positiva rispetto al pezzo, in quanto il
materiale caricato negativamente subisce un'erosione
superiore. Quando elettrodo e pezzo sono
sufficientemente vicini, tra i due si innescano delle
scariche che erodono il pezzo in modo complementare
rispetto alla forma dell'elettrodo. La scelta del
materiale dell'elettrodo e il controllo delle
caratteristiche delle scariche permettono di ottenere un
forte squilibrio tra l'erosione dell'elettrodo (usura
dell'utensile) e erosione del pezzo (lavorazione), a
favore di quest'ultimo. Man mano che il pezzo viene
eroso, l'elettrodo viene fatto avanzare, fino al
completamento della lavorazione. Durante la lavorazione,
l'elettrodo non entra mai in contatto con il pezzo, in
quanto una cosa simile crea un cortocircuito che
impedisce la creazione della scintilla.
Eccezionalmente, può essere applicata una polarità
invertita rispetto a quanto precedentemente detto:
ovvero applicare all'elettrodo una polarità negativa
rispetto al pezzo. Questo avviene per lavorazioni
particolari, come accoppiamenti di semistampi (dove
l'erosione viene equiripartita tra i due elementi) o
forature tramite elettroerosione (dove l'elettrodo viene
totalmente consumato).
Nella lavorazione non vengono creati normali trucioli: i
residui della lavorazione vengono chiamati sfridi e
assumono l'aspetto di microscopiche palline di metallo
che si disperdono nel dielettrico.
La presenza di un dielettrico è fondamentale per la
funzionalità della tecnologia, ed assolve vari scopi:
permette il controllo della localizzazione della
scintilla;
fornisce ioni per la generazione della scarica;
rimuove gli sfridi di lavorazione;
raffredda elettrodo e pezzo.
Perché la tecnologia possa funzionare correttamente, è
necessario il controllo delle caratteristiche delle
scintille. Infatti la scarica non è generata in maniera
continua, ma consiste in una successione di
micro-scariche prodotte da appositi dispositivi
elettronici in grado di generare treni di impulsi
controllati. I principali parametri elettrici
controllati sono:
tensione d'innesco; tipicamente alcune centinaia di
volt.
polarità; normalmente elettrodo positivo e pezzo
negativo.
corrente massima della scintilla; compresa tra 1 e 500
ampere.
durata della scintilla; compresa tra 1 micro-secondo e 2
milli-secondi.
pausa tra una scintilla e la successiva, compresa tra 1
e 30 micro-secondi.
Principio fisico
L'elettroerosione lavora sulla capacità termomeccanica
delle scariche elettriche di erodere i materiali.
L'azione erosiva delle scariche si può dividere in fasi:
Applicazione tra elettrodo e pezzo di una forte
tensione. In questa fase si crea un forte campo
elettrico tra i due punti a minor distanza relativa (a
minor distanza elettrodo/pezzo).
Rottura del dielettrico e apertura di un canale di
scarica. In questa fase il forte campo elettrico
accelera alcuni elettroni del pezzo che attraversano il
dielettrico, questo genera un effetto valanga che rompe
l'isolamento del dielettrico proprio in corrispondenza
del punto dove il campo elettrico è più elevato. Si crea
così un canale a bassa resistenza dove la corrente
elettrica può passare.
Allargamento del canale di scarica e fusione del
materiale. L'urto degli elettroni accelerati con le
molecole di dielettrico, generano ulteriori elettroni
liberi e ioni positivi che fungono da portatori di
carica e vengono accelerati dal campo elettrico;
conseguentemente si crea una canale di plasma ad
altissima temperatura (migliaia di gradi) in grado di
condurre molta corrente elettrica. Con il persistere
della corrente di scarica, il canale tende ad allargarsi
intorno al punto iniziale. Le aree dell'elettrodo e del
pezzo a diretto contatto con il canale di plasma,
sottoposte al bombardamento dei portatori di carica e
alle alte temperature del canale, si fondono, creando
dei piccoli crateri di materiale fuso.
Interruzione della scarica e implosione del canale di
scarica. Interrompendo la corrente, il canale di plasma,
non più alimentato da fonti di energia esterne, implode.
Espulsione del materiale dal cratere. Venendo
improvvisamente a mancare la pressione sulla superficie
del cratere, il materiale fuso viene risucchiato fuori,
lasciando il cratere vuoto. Il materiale fuoriuscito si
raffredda, solidificandosi in minuscole palline
(sfridi).
Applicazioni
L'elettroerosione si può dividere in sottotipi a seconda
dell'applicazione:
elettroerosione a tuffo; in questa applicazione la
lavorazione ha come scopo principale lavorare il pezzo
facendogli assumere una forma complementare rispetto
all'elettrodo.
Il ciclo di lavorazione va' diviso in due fasi:
creazione di un elettrodo di forma 'negativa' rispetto
alla forma della lavorazione che si vuole ottenere;
elettroerosione del pezzo con l'elettrodo
precedentemente creato, ottenendo così in 'positivo' la
forma voluta.
elettroerosione a filo; in questa applicazione, un filo
conduttore teso è usato come elettrodo per tagliare o
profilare il pezzo da lavorare.
Il filo (immagazzinato in una bobina) viene cambiato di
continuo durante la lavorazione, in quanto, essendo
sottoposto all'usura delle scariche e allo stress di
dilatazione, finirebbe per spezzarsi spesso,
interrompendo la lavorazione.
foratura per elettroerosione; in questa applicazione un
tubo viene usato come elettrodo per forare il pezzo.
Vengono usati tubi (generalmente di piccolo diametro) in
quanto attraverso essi viene pompato del dielettrico,
necessario per asportare gli sfridi dal fondo della
foratura.
molatura per elettroerosione; in questa applicazione una
mola di materiale conduttore erode il pezzo, in modo
analogo ad una mola ad abrasione.
Un esempio d'uso di questa tipologia di tecnica, è
quello dell'affilatura di lame con denti di Widia o
diamante sinterizzato, materiali di cui è difficoltosa
(e costosa) la molatura con tecniche abrasive
tradizionali.
Elettrodi
Uno degli "attori" principali della lavorazione per
elettroerosione è l'elettrodo. Nella lavorazione "a
tuffo" il risultato della medesima è un negativo della
forma dell'elettrodo; mentre nella lavorazione "a filo",
l'elettrodo si comporta come un seghetto, tagliando il
pezzo.
Come già accennato, perché si possa fare una lavorazione
utile, è necessario ridurre l'usura al minimo. Per far
ciò, oltre al controllo dei parametri elettrici, è
necessario partire da una corretta scelta del materiale
dell'elettrodo.
Materiale per elettrodi EDM
Per la lavorazione "a tuffo" bisogna cercare un
materiale che:
resista alle scariche;
sia facilmente lavorabile;
sia di costi contenuti.
Gli ultimi due aspetti sono particolarmente importanti
nella lavorazione a tuffo, in quanto la lavorazione che
si vuole ottenere richiede la realizzazione di una sua
esatta copia-elettrodo in negativo. In casi estremi, con
realizzazioni di stampi per plance o scocche plastiche,
potrebbe essere necessario realizzare elettrodi sagomati
e/o alettati di centinaia di chili.
L'esperienza ha portato alla diffusione di due tipi di
materiale: la grafite e il rame.
La grafite resiste bene alle scariche (per via dell'alto
punto di fusione), è relativamente facile da lavorare e
costa poco. Di contro, la grafite durante la lavorazione
di parti sottili (alette, nervature, ecc..) tende a
scheggiarsi, inoltre le scariche tendono a rovinarne la
superficie, impedendo di realizzare superfici ben finite
(cioè con bassa rugosità).
Anche il rame resiste abbastanza bene alle scariche (la
sua alta conducibilità termica tende a dissipare il
calore delle scariche), si può lavorare molto facilmente
(permettendo di realizzare particolari estremamente
fini) e le scariche rovinano poco la sua superficie,
permettendo lavorazioni particolarmente rifinite (in
qualche caso sino alla lucidatura). Di contro, il rame
non resiste altrettanto bene con alte correnti di
scarica (tipiche della lavorazione di sgrossatura) e
ovviamente è un materiale costoso.
Quando possibile, si consiglia così di realizzare due
elettrodi: un elettrodo di grafite per le lavorazioni di
"sgrossatura" e un elettrodo in rame per la lavorazione
di "finitura".
STAMPA
SABBIATRICI - ELETTROEROSIONE

TORNA
MENU GLOSSARIO
Da
Wikipedia, l'enciclopedia libera.
La fresatura è una
lavorazione meccanica a freddo per asportazione di
truciolo, che permette di realizzare un pezzo finito, la
cui forma è stata definita a progetto, partendo da un
pezzo grezzo di metallo e asportando il materiale in
eccesso, che è detto sovrametallo. Per poter realizzare
il pezzo finito è necessario che questo possa essere
inscritto nel pezzo di partenza da cui verrà asportato
il sovrametallo.
Descrizione
La lavorazione viene effettuata mediante utensili detti
frese, montate su macchine utensili quali fresatrici o
fresalesatrici.
La fresatura, a differenza di altre lavorazioni più
semplici, richiede la rotazione dell'utensile e la
traslazione del pezzo: i taglienti della fresa,
ruotando, asportano metallo dal pezzo quando questo
viene a trovarsi in interferenza con la fresa a causa
della traslazione del banco su cui il pezzo è ancorato.
Il ciclo lavorativo prevede normalmente una prima fase
di sgrossatura, in cui l'asportazione viene fatta nel
modo più rapido e quindi più economico possibile,
lasciando un sufficiente sovrametallo per la successiva
fase di finitura in cui si asportano le ultime parti
eccedenti per raggiungere le dimensioni previste
ottenendo una superficie più liscia. La finitura, che
consiste in una asportazione limitata di metallo,
consente di rispettare il progetto per quanto riguarda
le tolleranze delle dimensioni e il grado di rugosità
delle superfici.
I parametri
I principali parametri di lavoro della fresatura sono la
velocità di taglio, da cui si ricava la velocità di
rotazione della fresa, e l'avanzamento del pezzo:
La velocità di taglio dipende dal materiale di cui è
composta la fresa (o gli inserti che ne costituiscono i
taglienti) e dalla durezza del materiale da lavorare.
Per lavorare acciaio dolce (carico di rottura 490 N/mm2)
le frese odierne fatte in Widia possono lavorare a
velocità di taglio di 140 m/min, o fino a 200 m/min se
dotate di ricoperture quali nitruro di titanio, la
velocità va ridotta per lavorare materiali più duri. La
velocità di rotazione (n) della fresa, in giri/min, si
calcola dividendo la velocità di taglio (vc*)
(moltiplicata 1000) per la circonferenza della fresa in
mm (diametro Ø per 3,14):
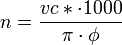
L'avanzamento si calcola moltiplicando il numero di
taglienti (z) per l'avanzamento per singolo tagliente
(fz*), per velocità di rotazione della fresa (n):

.
L'avanzamento per singolo tagliente è di norma 2/10 mm,
per taglienti a taglio perpendicolare al pezzo, può
essere aumentato per taglienti con geometria di taglio
inferiore ai 90°. Da ciò si capisce che l'avanzamento
dipende dalla geometria dei taglienti e dalla loro
densità, infatti frese con più taglienti ma di diametro
maggiore devono girare più piano, quindi z aumenta ma n
diminuisce.
Tuttavia la densità dei taglienti, cioè il loro numero a
parità di circonferenza della fresa, dipende dal
materiale da lavorare, in particolare dal tipo di
truciolo che produce: se si lavora l'alluminio la
densità sarà bassa per poter scaricare i trucioli che
sono lunghi e tendono ad aggrovigliarsi; la densità sarà
media per l'acciaio, mentre sarà maggiore per la ghisa
che produce trucioli in forma di polvere.
I parametri di lavoro sono indicati secondo la
simbologia ISO:
vc*(c* peduncolo) = velocità di taglio (m/min)
z = numero dei denti
n = velocità di rotazione (giri/min)
fz* = avanzamento al dente (mm/dente)
fn* = avanzamento al giro (fz* x z - mm/giro)
vf* = avanzamento al minuto (fz* x z x n; Oppure fn* x n
- mm/min)
STAMPA
SABBIATRICI - FRESATURA

TORNA
MENU GLOSSARIO
|
|